CLAREX Acrylic Light Guide Panels (LGP)
Custom-printed dot patterns designed for your specific lighting unit.
CLAREX Light Guide Panels are custom designed using the customer’s edge-lighting units. The factory designs a custom dot pattern which is then printed onto the CLAREX clear optical grade cast acrylic which has been machined to size. Uniformity and brightness of the backlights can be optimized regardless of lighting configuration. Custom Light Guide Panels are designed for each individual applications and are subject to development charges.
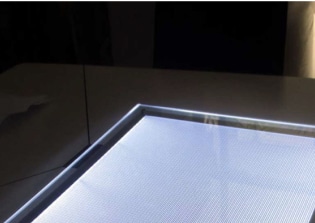
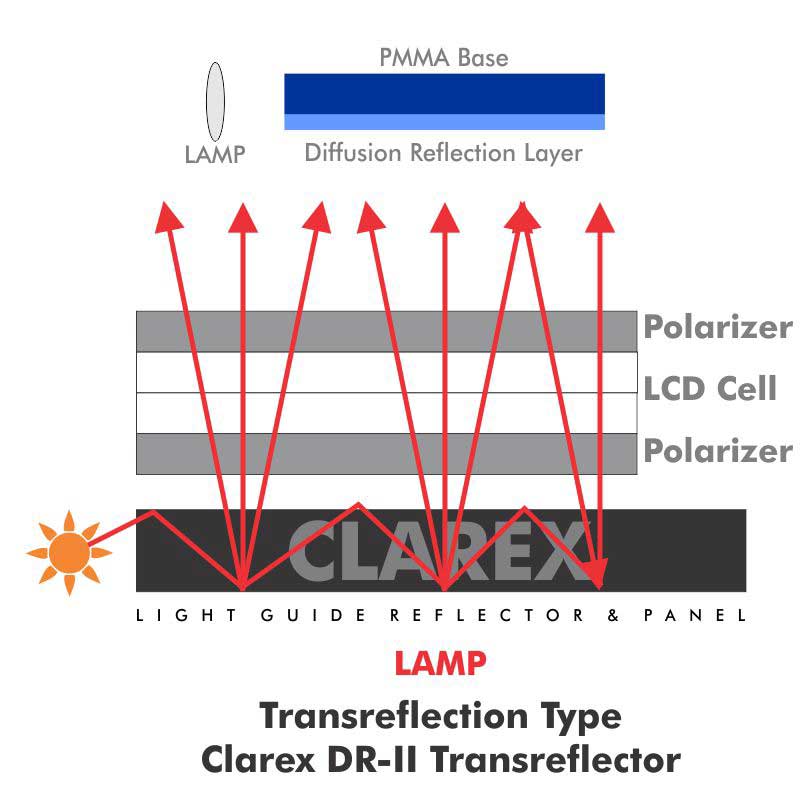
Applications
- Edge-lit LCD Backlights
- Selective backlighting, such as Keys on a Keyboard
Thicknesses
- From 0.2 to 5.0mm
- Needs to be thicker than the height of the light source
Size
Per customer specification
LGP Design Guidelines
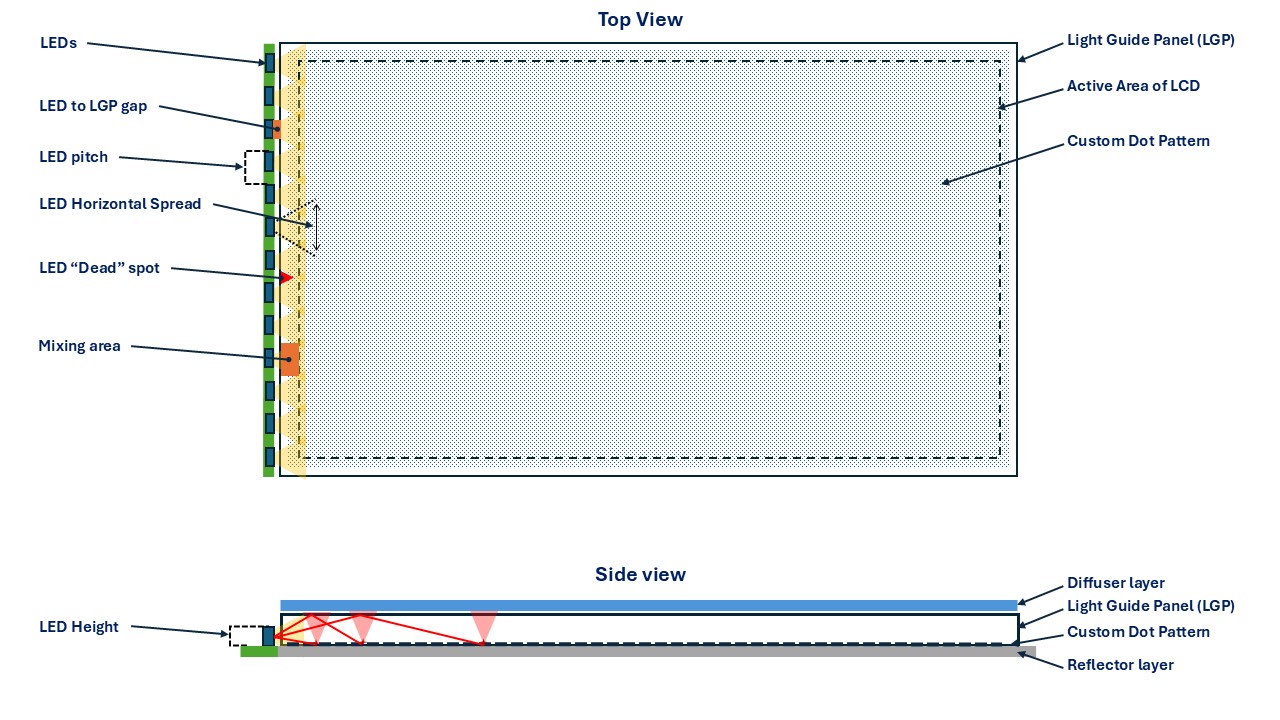
The factory can supply custom Light Guide Panels (LGPs) to work with customer supplied edge lighting units. Light is fired into the edge of the LGP and it will remain ‘captured’ within the sheet due to internal reflection, and will remain so until it either reaches the opposite side of the sheet, or if there is some ‘disturbance’ on the surface of the acrylic, such as a printed dot of reflective white ink.
- The CLAREX optical grade clear cast acrylic is used as the base substrate. It offers great long-path transmission through the material as well as improved thermal stability compared to commercial grade acrylic sheets.
- The factory designs a custom dot pattern based on the lighting unit configuration. Typically, the dot size and density increases the further they are from a light source.
- The dot pattern is silk screened onto the rear side of the clear acrylic using a special blend of reflective white ink.
- The factory will guarantee 70% uniformity using a standard 9-point measurement
- LGPs typically have a reflector layer behind it and a diffuser layer in front. These are not included with the custom LGPs. When stacked with the LGP, these layers should not make an optical bond.
- The gap between the LEDs and the LGP should be minimal. However, the LGP is acrylic and will expand when hot. So, it should be sized such that there is minimal gap when it is at its maximum expanded size while also considering the tolerance stack of the lighting unit. There needs to always be some gap, because if the LGP is restricted from expanding outwards, it will bow out in the center.
- The LEDs will have a specific horizontal luminous spread angle. When considering the pitch (separation) between the LEDs and the horizontal spread angle, there could be “dead spots” along the edge. While the factory could illuminate these areas to some extent by adjusting the dot pattern, it is best if they are not within the active area.
- It is best to have some mixing area between the edge of the LGP and the active area. But there are no suggestions for how much. Per the note above, aim to at least have the LED spread overlapping in the active area. Again, the factory can adjust the dot pattern accordingly in situations where there is minimal space for mixing.
- The factory can design the dot pattern for the specific lighting configuration, whether it is lit on 1, 2, 3, or 4 sides. There is no preferred/suggested configuration.
- Mirror tape is often used on unlit edges opposite a lit edge. The idea is that any light reaching the opposite edge will be reflected back into the LGP. This works to some degree, but the factory argues that the effect is not so great and may not be worth the extra cost. This is partially due to the losses as the light transmits (2 times) through the mirror tape adhesive.
- While a polished edge on the LGP would seem more efficient, the factory has found that a clean machined edge actually works better. The machined surface helps to slightly diffuse the light.
- The factory does not have experience with using diffuser tape/film along the lit edges of the LGPs. It might help improve uniformity in some situations (like minimal mixing area), but at what cost to brightness?
- The thickness of the light guide needs to be greater than the height of the LED. The factory recommends approx. 30% higher than the LED or 0.5mm, whichever is lower. A thicker LGP will be slightly more efficient and may be a better choice for larger LGPs. But as the LGP gets thicker, a larger mixing area will be required.
- In cases where there are two sets of emitters, such as Day and Night mode, the customer must choose a primary mode which the factory will use for the basis for the dot pattern design. After the dot pattern is setup for the primary mode, the factory can try to alter it to improve the uniformity of the secondary mode. But the result is typically that the uniformity of the secondary mode is not great. In these situations it is best to configure the two sets of lights such that the dot pattern will at least