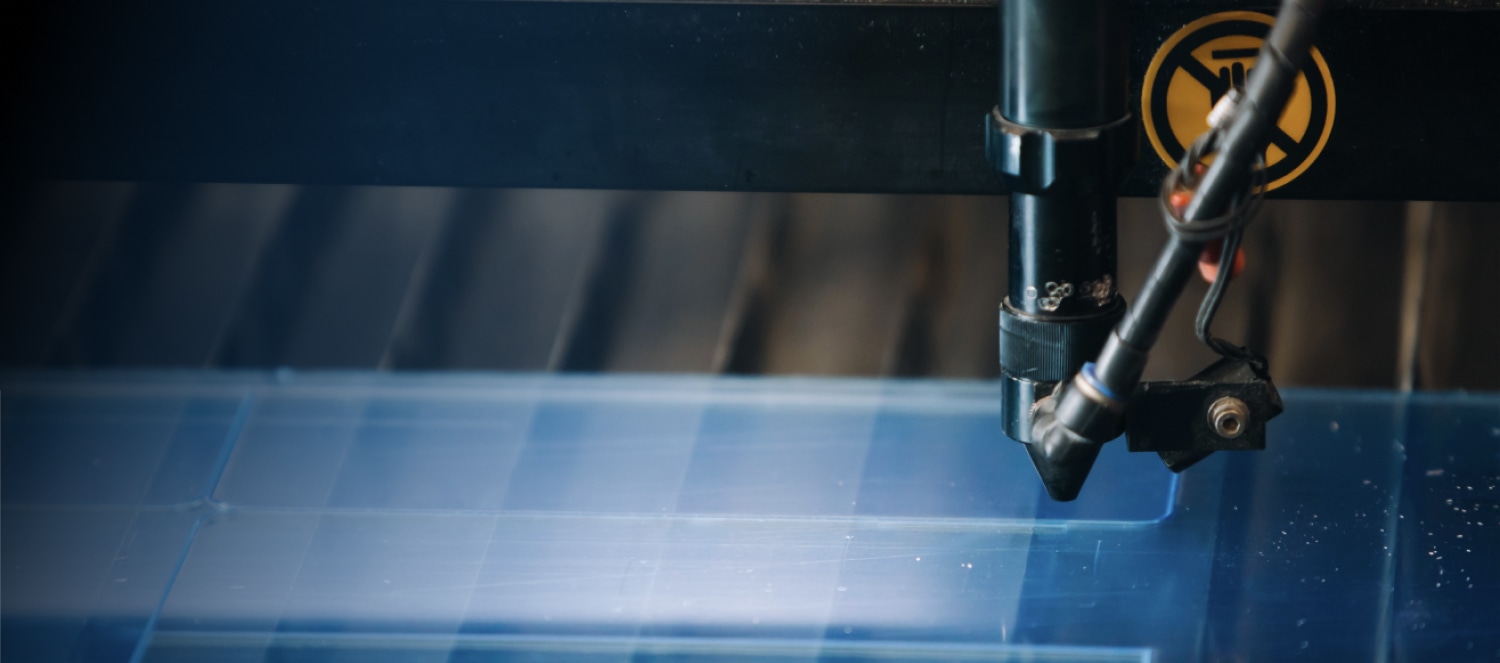
Why CLAREX
What is it about CLAREX Acrylic that makes it different?
CLAREX is the Clear Choice for Unique and Demanding Applications
CLAREX stands out as the industry leader for the highest quality acrylic sheets. Known for its superior optical properties, unmatched quality, and wide variety of customizable features, CLAREX custom optical grade cast acrylic products are trusted across industries like automotive, aerospace, medical, industrial, and consumer electronics. It is the top choice, and often the only choice, for demanding applications requiring unique material configurations and/or top quality. It’s no surprise that you can find CLAREX products used in products from the deepest depths of the oceans, to outer space, and everywhere in between!
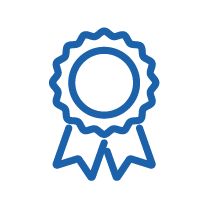
Unmatched Optical Quality
- Crystal-clear transparency with superior light transmission.
- Distortion-free viewing for precision applications.
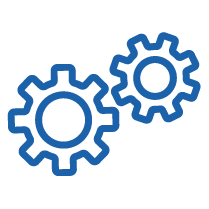
Durability and Longevity
- Exceptional resistance to UV degradation for outdoor use.
- Impact-resistant material that ensures long-lasting performance.
- Scratch-resistant coatings available for demanding environments.
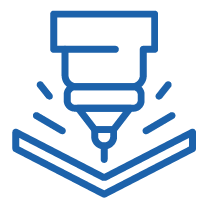
Versatile Applications
- Perfect for industries like automotive, aerospace, medical, and consumer electronics.
- Customizable for displays, lenses, signage, and protective covers.
- Lightweight alternative to glass without compromising strength or clarity.
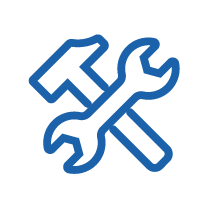
Innovative Customization Options
- Wide range of thicknesses, colors, and surface finishes.
- Ability to add custom tints, coatings, or texturing for specific needs.
- Precision fabrication capabilities, including CNC laser cutting and routing.
- Finished parts could be supplied with adhesives and printing.
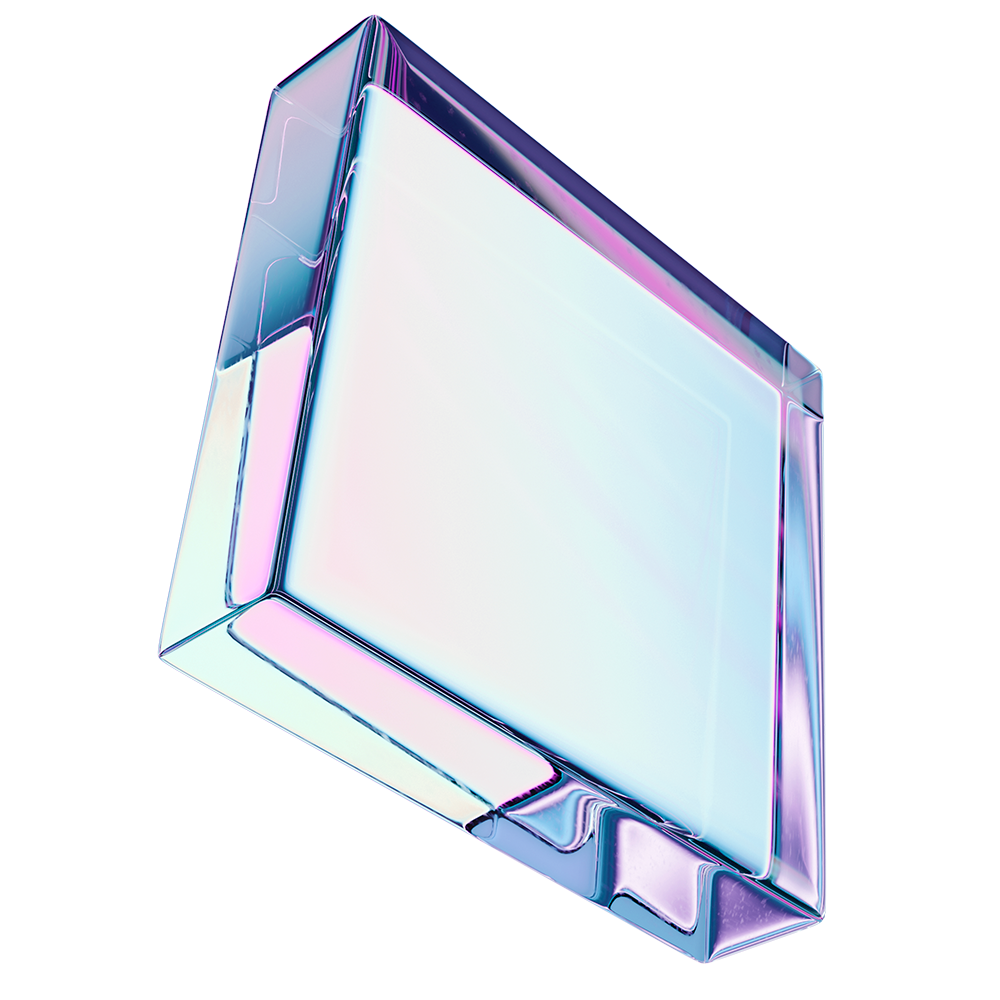
The Manufacturing Process
Extruded vs. Cell-Cast Acrylic: What is the difference?
To understand what sets CLAREX apart from other Acrylic (PMMA) options, it is best to first discuss the two main options for manufacturing acrylic sheets: Casting and Extrusion
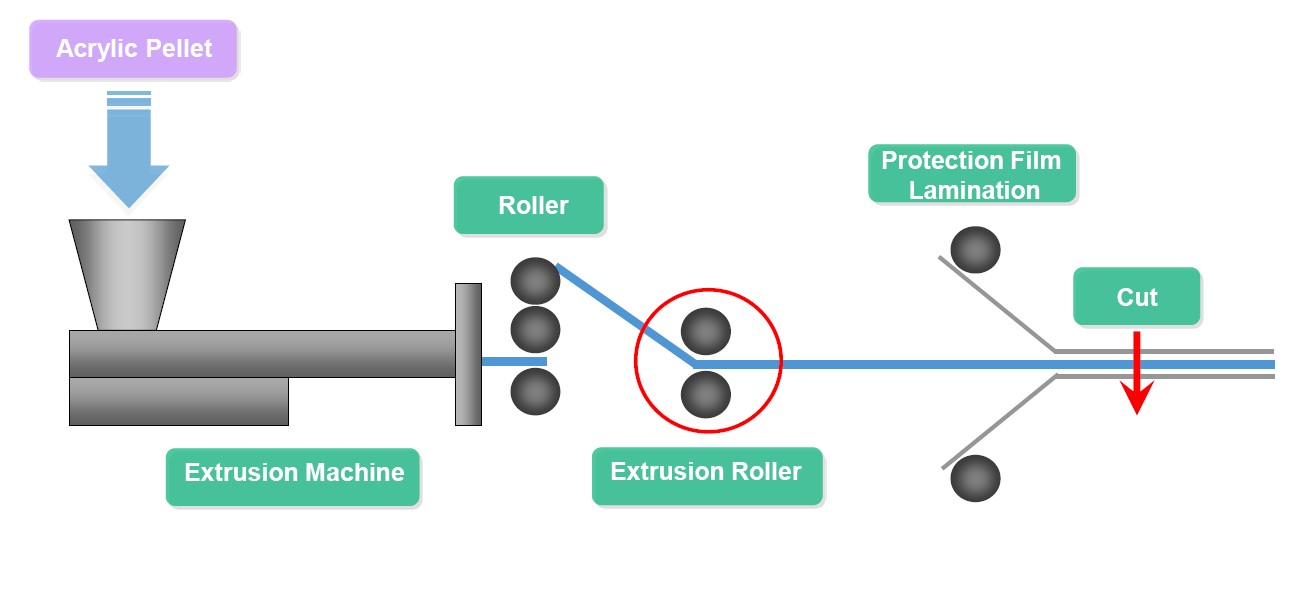
Standard Extrusion Process
- Starts with small acrylic pellets or liquid resin
- The pellets are melted and squeezed through dies
- A continuous sheet of acrylic comes out from the die
- The sheet travels over and through a range of rollers to help smooth (or texture) the surface as the sheet cools
- The long continuous sheet is cut down into individual sheets, or in some cases could be rolled onto a reel
- Common tradenames are Optix Lucite, Acrylite, & Plexiglas
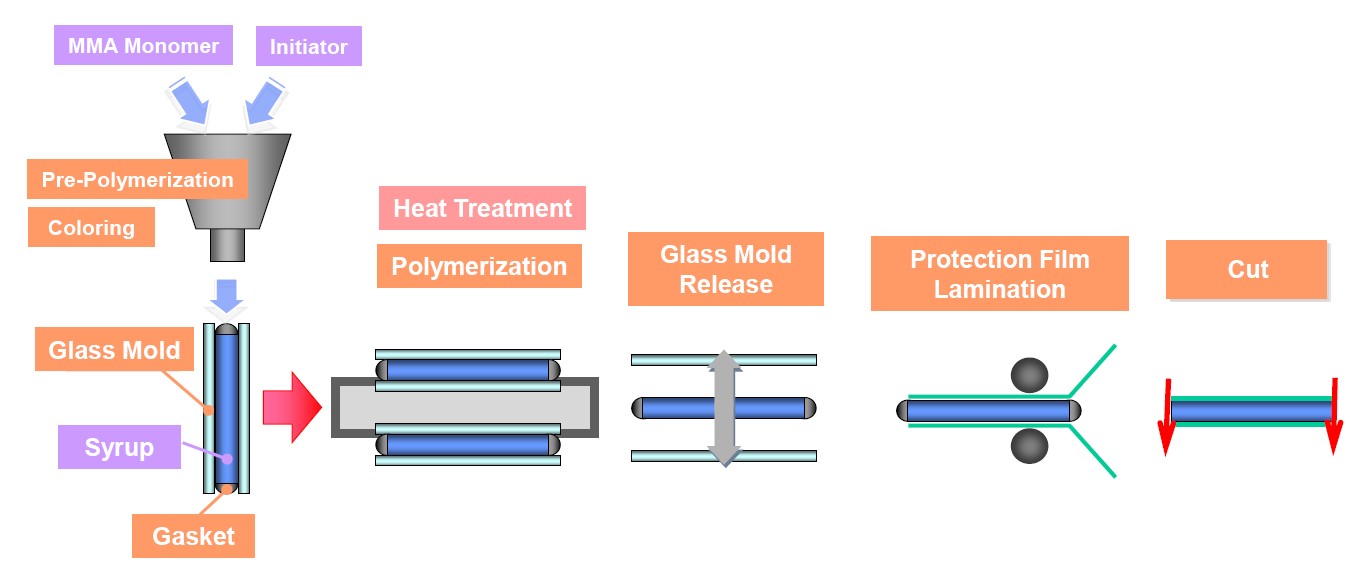
Standard Cell-Cast Process
- Starts with liquid methyl methacrylate (MMA monomer)
- The monomer is poured into a mold with an initiator
- The monomer polymerizes (hardens) into polymethyl methacrylate (PMMA) within the temperature-controlled molds
- Upon completion of the polymerization process, the individual sheets of Acrylic/PMMA are removed from the molds
- Common tradenames are Lucite, Acrylite, Chemcast, Polycast, Perspex, & Astariglas
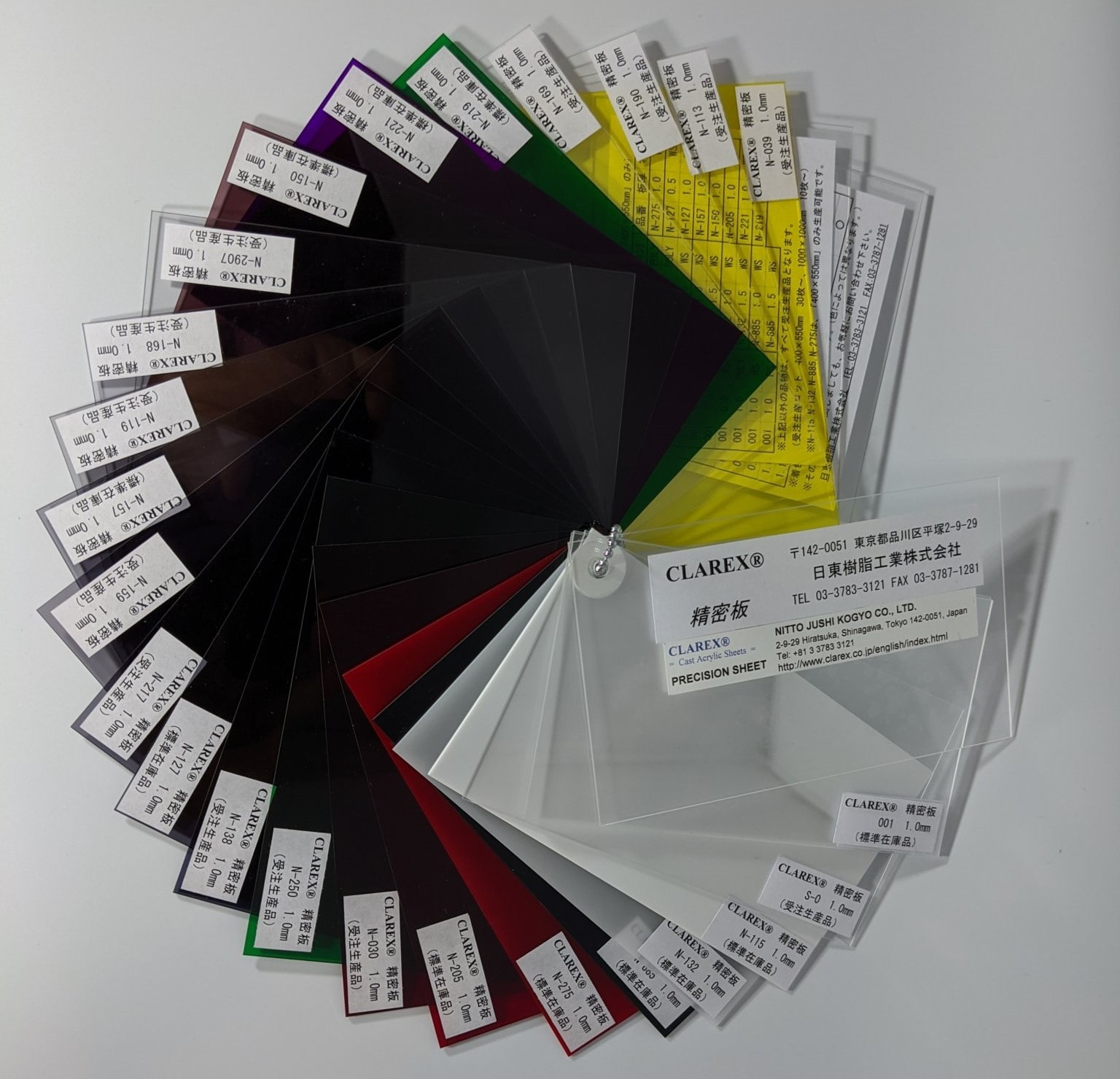
What is CLAREX doing differently?
CLAREX Cell-Cast Acrylic
CLAREX takes the standard cell-casting process to the next level with advanced techniques that ensure unmatched quality and performance. By refining every step of the manufacturing process, CLAREX delivers superior optical and mechanical properties.
- Highly Polished Mold-Sets are used to ensure the surface roughness and wavefront distortion are minimized
- Pure Monomer is used, resulting in minimal haze, minimal auto-fluorescence, and minimal inclusions while maximizing long-path transmission
- The process has been optimized to yield sheets with High Molecular Weight which improves the acrylic’s temperature and chemical resistance
- Relatively Tight Thickness Tolerances are achieved through accurate metering of monomer and process controls
- Hardcoat can be applied in-mold, a unique capability, resulting in the best optical quality hardcoat available
- Finished sheets are 100% Visually Inspected to ensure that they are defect-free prior to applying protective masking
How do the different acrylic sheet manufacturing methods compare?
Extruded Acrylic | Cell-Cast Acrylic | CLAREX Cell-Cast Acrylic | |
---|---|---|---|
Optical Quality | Good, but prone to inclusions | Better optical clarity, but prone to inclusions | Optical grade material 100% visually inspected to 80/60 Scratch/Dig Specs |
Surface Quality | Good, but prone to surface imperfections | Better | Best. Highly polished molds are used resulting in extremely low surface roughness and low wavefront distortion |
Mechanical Properties | Softer. Makes it more impact-resistant but more susceptible to scratches | Harder. More rigid and scratch-resistant | Harder. More rigid and scratch-resistant |
Birefringence | Will be an issue due to the internal stresses from the extrusion process | Low/none due to the low internal stresses in the casting process | Low/none due to the low internal stresses in the casting process |
Auto-Fluorescence | Will be an issue due to impurities within the sheets | Will be an issue due to impurities within the sheets | Very low due to the use of ultra-pure monomer |
Molecular Weight | Low | High. About 2x extruded acrylic | Very High. About 2x standard cast acrylic and 4x standard extruded acrylic |
Thermal Stability | Lowest. Can warp or melt when fabricated | Good. Machines well | Best due to high molecular weight |
Chemical Resistance | Lowest | Good | Best due to high molecular weight |
Thickness Range | Typically 0.8 – 12.0mm 0.031 – 0.477″ | Typically 3.0 – 25.0mm 0.118 – .976″ | 0.2 – 5.0mm 0.008 – 0.197″ |
Thickness Variation | Generally +/-10%, but will typically be very consistent within each sheet and from sheet to sheet within a production lot | Generally +/-15-20%. The thickness will vary within each individual sheet | Generally +/-10%. The thickness will vary within each individual sheet |
Customization | Limited customizations are available and would require huge minimum order quantities | Limited customizations are available and would require significant minimum order quantities | Wide range of customizations available. Custom sheets can be made in low volumes, down to a single sheet |
Hardcoat Options | Hardcoat could be added as a secondary process (flow or dip coat). Prone to surface defects | Hardcoat could be added as a secondary process (flow or dip coat). Prone to surface defects | Hardcoat could be added during the casting process (in-mold) resulting in an optical grade defect-free hardcoat that will not delaminate |
Nonglare Surface Texture Options | Few available. May require large MOQs | Few Available. Typically more for aesthetics (heavy matte and frost) | Many textures ranging from High Gloss to Heavy Matte |
Machinability | Prone to melting/chipping during CNC machining. Can craze in laser cut heat effect zone | Machines and Laser Cuts well | Machines and Laser Cuts well |
Cost | Lowest Cost | Medium Cost | Highest Cost |
Applications | Typically used in applications where cost is critical and an off-the-shelf extruded sheet meeting the project requirements is available | Typically used when optical quality or machinability are critical, or when thick or colored sheets are needed | Typically used when the application requires the highest quality material properties, or when a material configuration is needed which cannot be found off-the-shelf elsewhere |
Is acrylic the best choice for your application?
CLAREX Acrylic vs. Polycarbonate & CR-39: A Side-by-Side Comparison
While CLAREX Cell-Cast Acrylic is a great choice for many applications, is it the best choice for yours? Let’s take a look at how the CLAREX cast acrylic compares to other plastic materials used for optical filters. Typically that would include polycarbonate (PC) and CR-39. When choosing the right material for your optical applications, it’s essential to compare the strengths and weaknesses of each option.
Polycarbonate (PC) | CR-39 | CLAREX Acrylic | |
---|---|---|---|
Manufacturing Process | Extrusion | Cell-Casting | Cell-Casting |
Common Tradenames | Lexan, Makrolon, Tuffak | Homalite, PADC (Polyallyl diglycol carbonate) | CLAREX! |
Optical Quality | Relatively low. Will have lower transmission, higher haze, and prone to inclusions | Better optical clarity, but prone to inclusions | Optical grade material 100% visually inspected to 80/60 Scratch/Dig Specs |
Surface Quality | Good, but prone to surface imperfections | Better | Best. Highly polished molds are used resulting in extremely low surface roughness and low wavefront distortion |
Mechanical Properties | Very soft. Makes it more impact-resistant but extremely susceptible to scratches and abrasion | Harder. More rigid and scratch-resistant | Harder. More rigid and scratch-resistant |
Birefringence | Will be an issue due to the internal stresses from the extrusion process | Low/none due to the low internal stresses in the casting process | Low/none due to the low internal stresses in the casting process |
Auto-Fluorescence | Will be an issue due to impurities within the sheets | Low | Very low due to the use of ultra-pure monomer |
Thermal Stability | Best. Can withstand the highest temperatures | Better | Good due to high molecular weight |
Chemical Resistance | Lowest | Best | Better |
Flame Resistance | Varies, but available up to V-0 UL rating | UL 94HB | UL 94HB |
Thickness Range | Wide range from thin films up to 1″ thick sheets | Typically 0.8 – 12.0mm 0.031 – .472″ | 0.2 – 5.0mm 0.008 – 0.197″ |
Thickness Variation | Generally +/-10%, but will typically be very consistent within each sheet and from sheet to sheet within a production lot | Generally +/-15-20%. The thickness will vary within each individual sheet | Generally +/-10%. The thickness will vary within each individual sheet |
Customization | Limited customizations are available and would require large minimum order quantities | Limited range of customizations available. Custom sheets can be made in low volumes, down to a single sheet | Wide range of customizations available. Custom sheets can be made in low volumes, down to a single sheet |
Hardcoat Options | Hardcoat could be added as a secondary process (flow or dip coat). Prone to surface defects | Hardcoat could be added as a secondary process (flow or dip coat). Prone to surface defects | Hardcoat could be added during the casting process (in-mold) resulting in an optical grade defect-free hardcoat that will not delaminate |
Nonglare Surface Texture Options | Few available. May require large MOQs | Few Available | Many textures ranging from High Gloss to Heavy Matte |
Machinability | Machines well, but prone to melting if feeds/speeds are not dialed in. Doesn’t laser cut well (burns) | Can be machined with proper tooling, but prone to chipping. Can be laser cut, but results in sticky edges and strong odors | Machines and Laser Cuts well |
Cost | Lowest Cost | High Cost | High Cost |
Availability | The basic range of PC materials can be found at most plastics distributors | CR-39 is not easy to find. Typically needs to be made to order | Astra Products has a wide variety of CLAREX materials in stock at our warehouse in New York. If we don’t have what you need in stock, we can typically get it for you within 4-8 weeks |
Applications | Typically used in applications where the filters need max impact resistance, max flame resistance, and/or operate at high temperatures | Typically used when optical quality is critical, or when thick or colored sheets are needed | Typically used when the application requires the highest quality material properties, or when a material configuration is needed which cannot be found elsewhere |
Customization
Custom sheets & parts to meet your application
Do you have a unique design requirement? We can help! Choose the thickness, formulation, additives, color dye/pigments, surface textures, surface coatings, and optical coatings for your custom material configuration, and if we don’t already have it in stock at our warehouse in New York, we can typically have it ready for you in 4-8 weeks. We can even fabricate the finished parts for you.
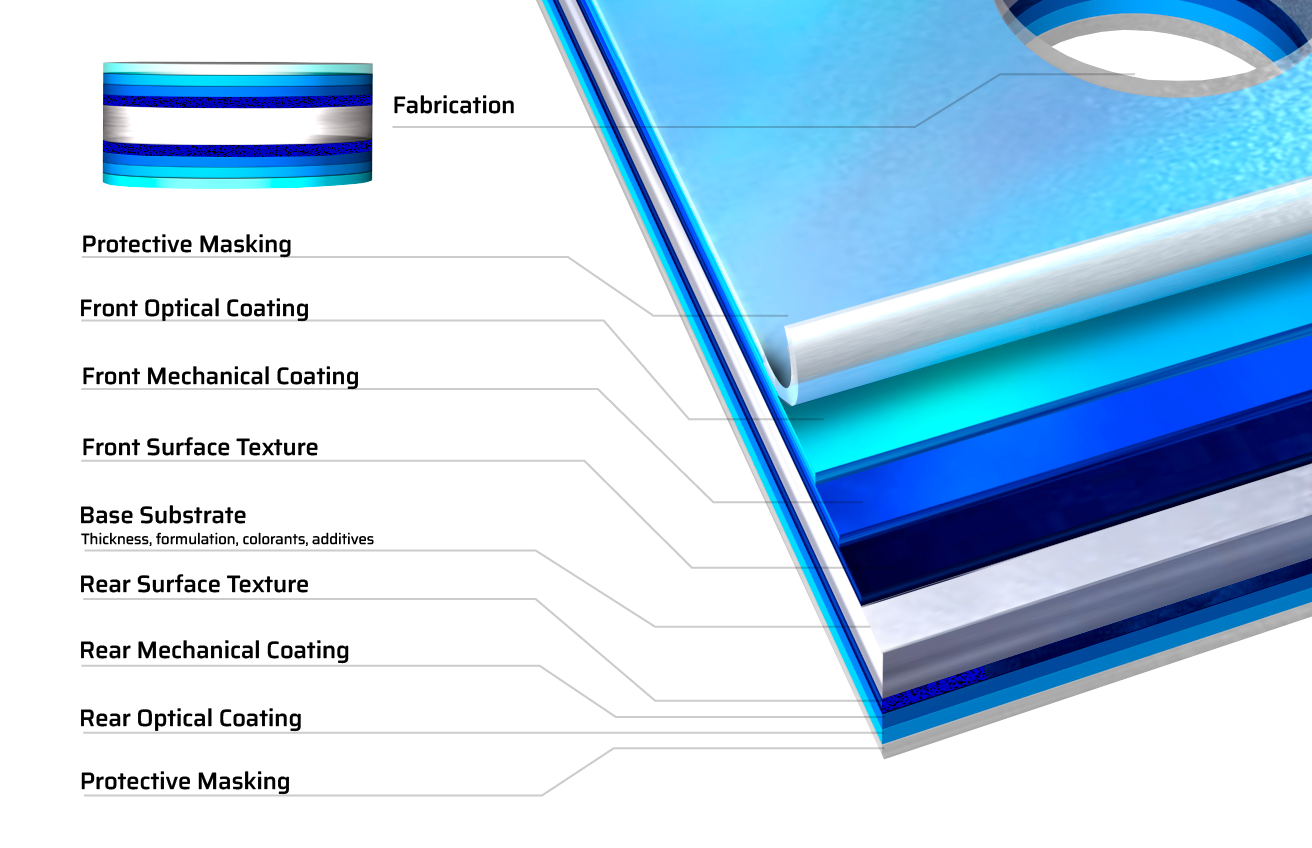
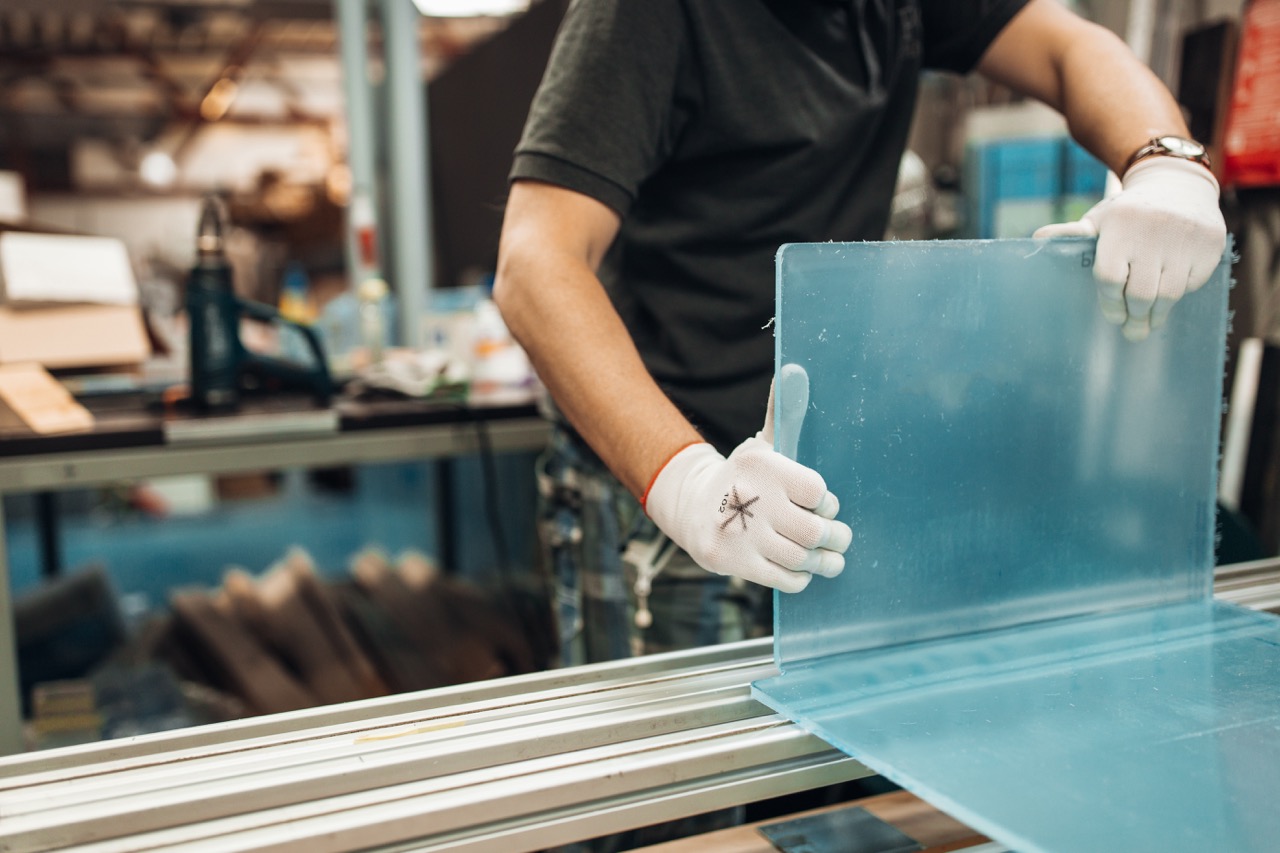
CLAREX QUALITY
Uncompromising Quality Control for Every CLAREX Product
Every CLAREX product undergoes stringent quality control and inspection processes, such as 100% visual inspection to ensure it meets the highest standards for cosmetic quality and performance. Our commitment to excellence sets us apart in the industry.
Working with astra
Why Choose Astra
When purchasing CLAREX materials from Astra Products, you are working with the Exclusive North American CLAREX sales agent. We have been working with Nitto Jushi Kogyo (NJK) since 1977 and have built a reputation as a trusted name in distributing and fabricating CLAREX products, offering extensive expertise and unparalleled customer service. We provide genuine CLAREX materials tailored to your specific needs, backed by our and NJK’s commitment to quality and reliability. That includes Astra’s ISO and IATF quality certifications as well as NJK’s. From personalized support to efficient supply chain management, Astra Products ensures you get the best solutions for your applications.
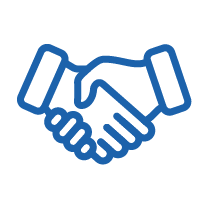
Trusted Expertise
Knowledgeable team to guide you from product selection to delivery.
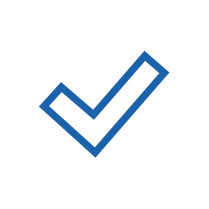
Reliable Supply Chain
Direct access to genuine CLAREX materials for quality assurance & efficient logistics and fast shipping to meet project deadlines.
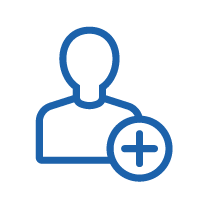
Customer-Centric Approach
Tailored solutions to meet unique project requirements and technical support for seamless integration into your projects.
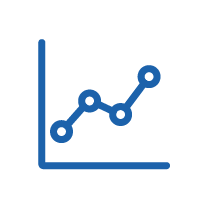
Proven Track Record
Long-standing relationships with leading manufacturers across industries proven by our history of success.
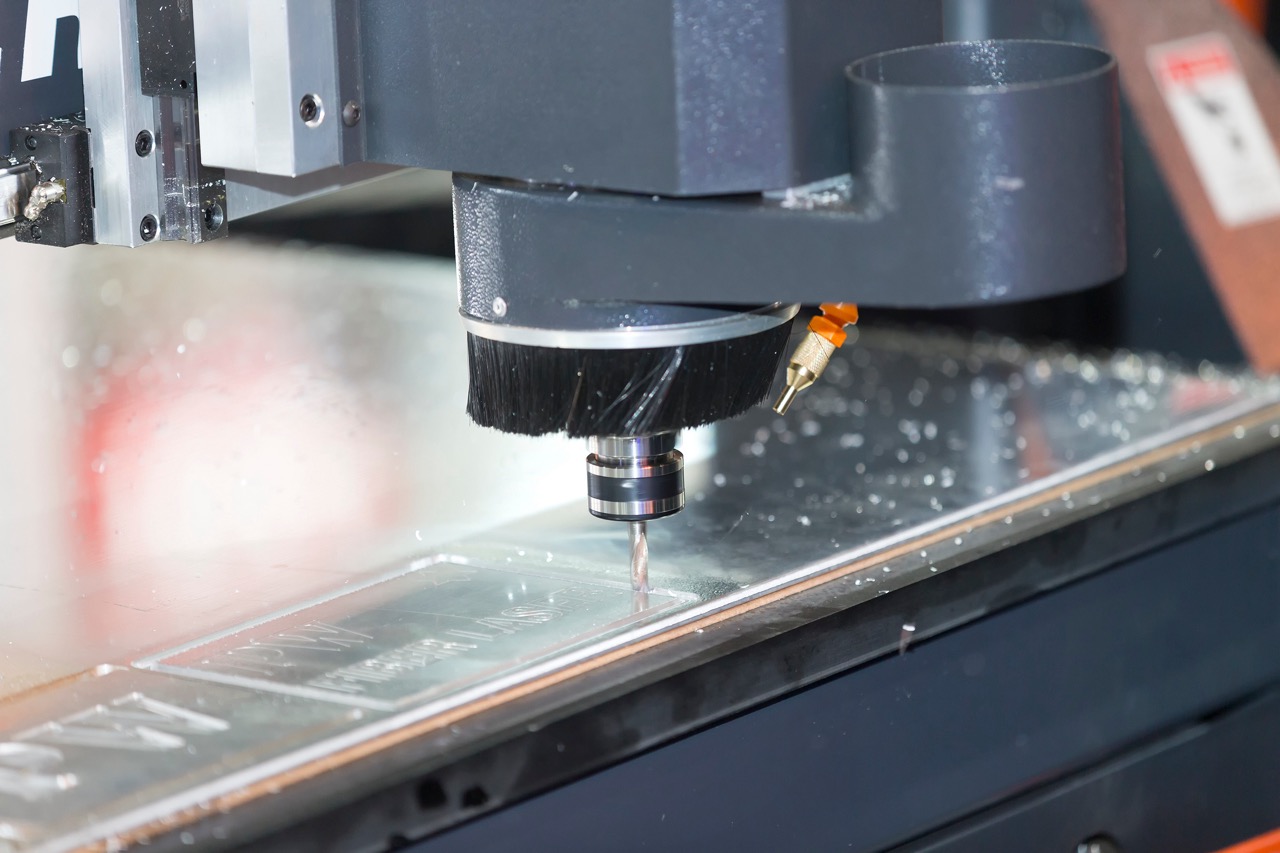